Restructuring of a sintered metal area, resulting in an annual saving of $ 13M
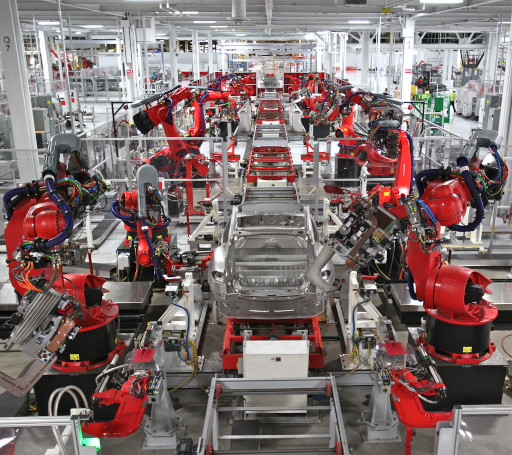
Manager:
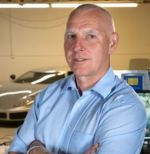
Mr.W. B.
-
Customer:
Confidential
-
Role:
Plant Manager
-
Location:
USA
-
Turnover:
Sales: Business area wide $ 550M / year in 2008
-
Time frame:
6 Month
-
No. of employees:
worldwide 2000 in 20 locations
About the Customer
- The company is a global automotive company with direct contact to automakers (Tier1) headquartered in the US. The annual revenue is approximately $ 5 billion and the company is organized in a businessstructure. Worldwide employment includes approximately 16,000 employees in more than 60 locations. The company is in the active product segments either market leader or # 2 in the world market. The described business area is world market leader for its products.
Testimonial from Сustomer
The employees fully supported the activity with visible improvements in work ethic and product quality.The management was very satisfied with the improvement in the financial situation and the extremely short implementation time.
Situation (Challenge)
One of the production plants for powder metal components with 150 employees was losing money over a long time, but the product was important for the system and could not be easily outsourced due to technical complexity. After several team efforts to improve the situation Mr. W.B. (BU VP) took charge of the project and acted at the same time as a mentor for the plant manager.
Solution (Achievement)
On the basis of a thorough analysis of the business situation including the product portfolio,
the production key figures and the employment situation, an action plan with fundamental changes was
created and implemented. Improvements were achieved in all areas of the business in a short time.
The improvements included technical changes to products, adjustment of the product portfolio,
fundamental changes in the manufacturing process and the cancellation of loss-making machines.
Fundamental changes in production processes with complete change of material flow in production
were implemented. The action made 18 machines redundant. Most of the machines were offered and
sold on the market.
The action was carried out in six months and showed immediate improvements in the
financial situation.
Sustained cost savings of $ 13M per year were achieved.